A good fit for the Olympics
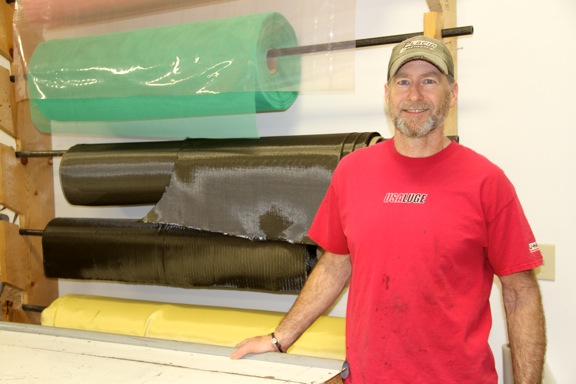
Placid Boatworks owner Joe Moore Wednesday, Feb. 14, poses next to the fiberglass (top), carbon (middle) and Kevlar (bottom) he uses for his canoes and the pods he makes for luge sleds used by athletes at USA Luge and other nations, such as India and Romania. (News photo — Andy Flynn)
LAKE PLACID – When Chris Mazdzer was competing at the Pyeongchang Winter Olympics – earning a silver medal at the end of his fourth run Sunday, Feb. 11 – Placid Boatworks owner Joe Moore saw something familiar.
It was the sled he helped build.
“I was watching Chris after the third run, and they pick up the sled after they’re done, and ours are very distinctive because you’ll see on the inside two strips of yellow on the sides and a strip of carbon black down the center,” Moore said.
Moore, who is usually busy making canoes, has been making the pods – or seats – for the sleds USA Luge builds for its athletes. He also makes pods for former USA Luge Olympian and technical director Duncan Kennedy, of Lake Placid, who operates Kennedy Racing Sleds and makes sleds for luge athletes from India and Romania.
When Moore saw a photo of six-time Olympian Shiva Keshavan of India going down the Pyeongchang sliding track, he shared the photo on his Facebook page.
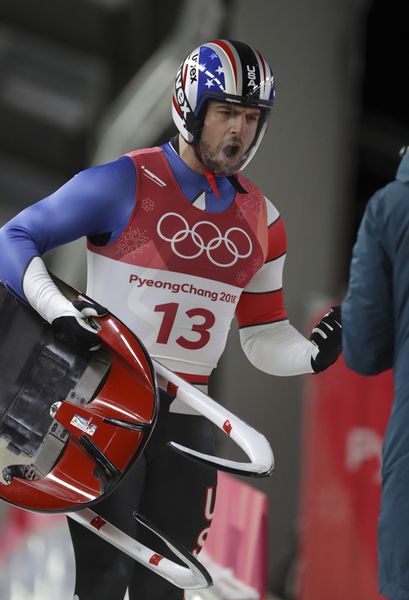
Chris Mazdzer of United States celebrates after finishing his second run in the men’s luge at the 2018 Winter Olympics in Pyeongchang, South Korea, Saturday, Feb. 10. The pod (seat) was manufactured by Placid Boatworks in Lake Placid. (AP Photo/Michael Sohn)
“Another athlete riding one of our sleds,” he wrote.
It was one of the pods made by Placid Boatworks. The sled was assembled by Kennedy.
Moore’s process for making the pods – vacuum-assisted resin transfer molding – starts with a variety of molds.
“We build all our boats the same way,” Moore said.
He places fabric inside the mold, primarily fiberglass, but they also put a little bit of carbon and Kevlar in there. Applying a vacuum around the perimeter of the mold, he introduces the resin down the center of the mold. It sets within about 15 minutes.
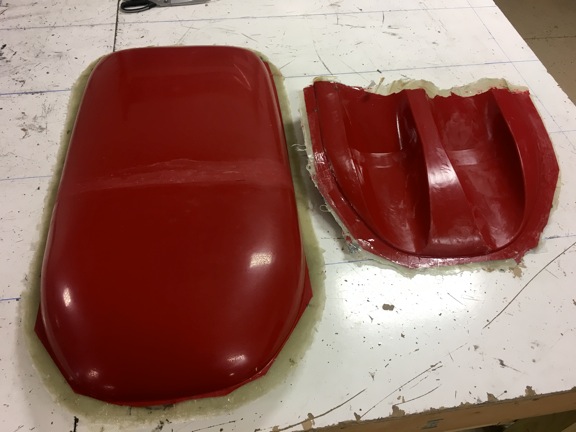
Here is a look at one of the luge pods after it is manufactured at Placid Boatworks in Lake Placid. (Photo provided)
The carbon fiber is black, very stiff and not as tough as the Kevlar, which is yellow, tough and resilient.
“You combine the two materials, and you get the best of both worlds,” Moore said. “You get the stiffness of the carbon and that toughness of the Kevlar.”
All the USA?Luge athletes are most likely riding pods made at the Placid Boatworks building on Station Street in Lake Placid.
“The pod is what we lay in. So that fits to our body,” Mazdzer told the News in October before the World Cup season began. “We’re holding on to handles in there. And what connects the pod to the runners and the kufens, the candy cane looking things, are the bridges.”
At their Church Street headquarters in Lake Placid, USA Luge athletes, coaches and technicians take the pods and attach them the kufens, with the steels at the bottom.
“We literally built a dozen pods for them this year,” Moore said.
Moore said Feb. 14 that he’s happy for Mazdzer.
“It’s nice to see that all the work that everybody has been putting in – both the athletes and the guys on the tech team – has paid off,” Moore said.
In October, Mazdzer hadn’t quite settled on a sled for the season. After a rough season the year before, he seemed frustrated.
“This year, I’ve tried three pods, broken a pair of kufens, used three others and have switched between four pairs of steels,” Mazdzer said.
By the time of the Olympics, Mazdzer had his sled worked out. The silver medal is a testament to all the tinkering and to the help he got from Moore back home.
- Chris Mazdzer of United States celebrates after finishing his second run in the men’s luge at the 2018 Winter Olympics in Pyeongchang, South Korea, Saturday, Feb. 10. The pod (seat) was manufactured by Placid Boatworks in Lake Placid. (AP Photo/Michael Sohn)
- Here is a look at one of the luge pods after it is manufactured at Placid Boatworks in Lake Placid. (Photo provided)